When people talk about battery materials, the discussion is often dominated by metals, such as lithium, cobalt, nickel and copper. Few understand or fully appreciate another important component: conductive additives. Every battery needs them, and some are better than others. This story will examine the various options and describe how high-quality additives make batteries more efficient, safe, long lasting and environmentally friendly. We will also explore how one industry leader — Orion S.A. — is taking an innovative approach in providing conductive additives to the lithium-ion battery industry.
How do batteries work?
To better understand how conductive additives work together with other materials in a battery, it helps to look at how batteries function. Put simply, a battery is a way of storing energy with chemicals. Most batteries have four main parts: a cathode (the positive electrode), the anode (the negative electrode), a separator in between the anode and cathode, and a chemical material called an electrolyte.
The basic principle of a battery is that it stores energy in the electrodes. When a battery is used, this stored chemical energy is converted into electrical energy. Electrons move from one electrode through the external circuit, like an electric motor, to the other electrode.
Meanwhile, inside the battery, only ions flow between the electrodes to keep the process going. To maximize the energy and power output of a battery, it’s crucial that electrons can flow with minimal resistance. However, most electrode materials have poor electrical conductivity, meaning they naturally have high resistance. To address this, conductive additives are incorporated into the electrode materials. These additives form conductive pathways that facilitate the efficient transfer of electrons during both charging and discharging, ensuring better battery performance and higher efficiency.
Carbon black
One of the most common types of conductive additives used in all commercial batteries is carbon black. It is a solid form of carbon produced as powder or pellets. For more than a century, carbon black has been used as a conductive additive in the negative electrode of lead-acid batteries for automotive batteries and industrial batteries. In recent years, demand has been growing among producers of lithium-ion batteries.
Almost all the carbon black in the world is produced with what is called the furnace process. The raw material used in the process is usually heavy oil or coal tar, which is heated in a furnace. This tends to be messy process with a large carbon footprint.
Some batteries use carbon nanotubes — hollow tubes made of rolled-up graphene sheets. They offer high conductivity; however, the production process also creates substantial pollution, and the materials are cumbersome to implement in battery manufacturing processes. This ultimately makes the material an expensive additive in the battery.
There is a much cleaner way to make a conductive additive. It involves using acetylene gas, which is virtually free of impurities. Acetylene gas is an industrial byproduct from the process of making ethylene, which is used in polyester fibers, films, plastics and other everyday materials.
Plants that make acetylene-based conductive additives for batteries are usually located near ethylene facilities, which supply the acetylene via a pipeline.
“The technology is much friendlier to the environment because when we make acetylene-based conductive additives, we use an industrial byproduct – acetylene gas – that is often burned for power generation, creating significant CO2 emissions,” said Dr. Adrian Steinmetz, global vice president for batteries at Orion S.A. “We repurpose and upcycle the material to make high-value additives that play a critical role in lithium-ion batteries that are key for the global shift to electrification.”
Orion’s competitors in China make acetylene-based conductives with acetylene made from calcium carbide feedstock, sourced from the coal industry. Compared with those products, Orion’s acetylene-based PRINTEX kappa 100 additive has an up to 90% lower carbon footprint.
Acetylene’s advantages
Plants that produce conductive additives with acetylene gas are virtually zero-waste facilities with minimal nitrogen oxides (NOx) and sulfur oxides (SOx) emissions. Orion’s acetylene process yields only 0.2 tons of CO2 per ton of product, compared with over 1.6 tons of CO2 per ton for the furnace process.
“In other words, approximately 90% of the carbon is retained in our product, resulting in a carbon footprint that is remarkably eight times lower than conductives made with the furnace process,” Dr. Steinmetz said.
Acetylene-based conductive additives have other significant advantages.
One advantage is that the material is hydrophobic and doesn’t absorb water.
“From a storage and handling perspective, this is beneficial for battery manufacturers because limiting moisture is important for the safety and lifespan of batteries,” said Dr. Steinmetz, who joined Orion last year to lead a new team for batteries.
Another important advantage for acetylene-based conductives is their high purity. The material has super low metal content and the lowest concentration of any other non-metallic impurities.
“This is critical for the longevity and safety of a lithium-ion battery,” Dr. Steinmetz said. “If the metal content is too high, you destroy the life of the battery and might create the risk of uncontrollable thermal runaway reactions. By using acetylene gas as a feedstock, we create a material with high purity and low metal concentrations, typically below five parts per million.”
Orion’s history
Orion’s corporate lineage stretches back more than 160 years to Germany, where the company has the longest-operating carbon black plant. The company has been supplying battery makers across the world for over a century. The car industry has long been one of Orion’s biggest customers, and about 75% of the company’s produced volume ends up in automotive applications.
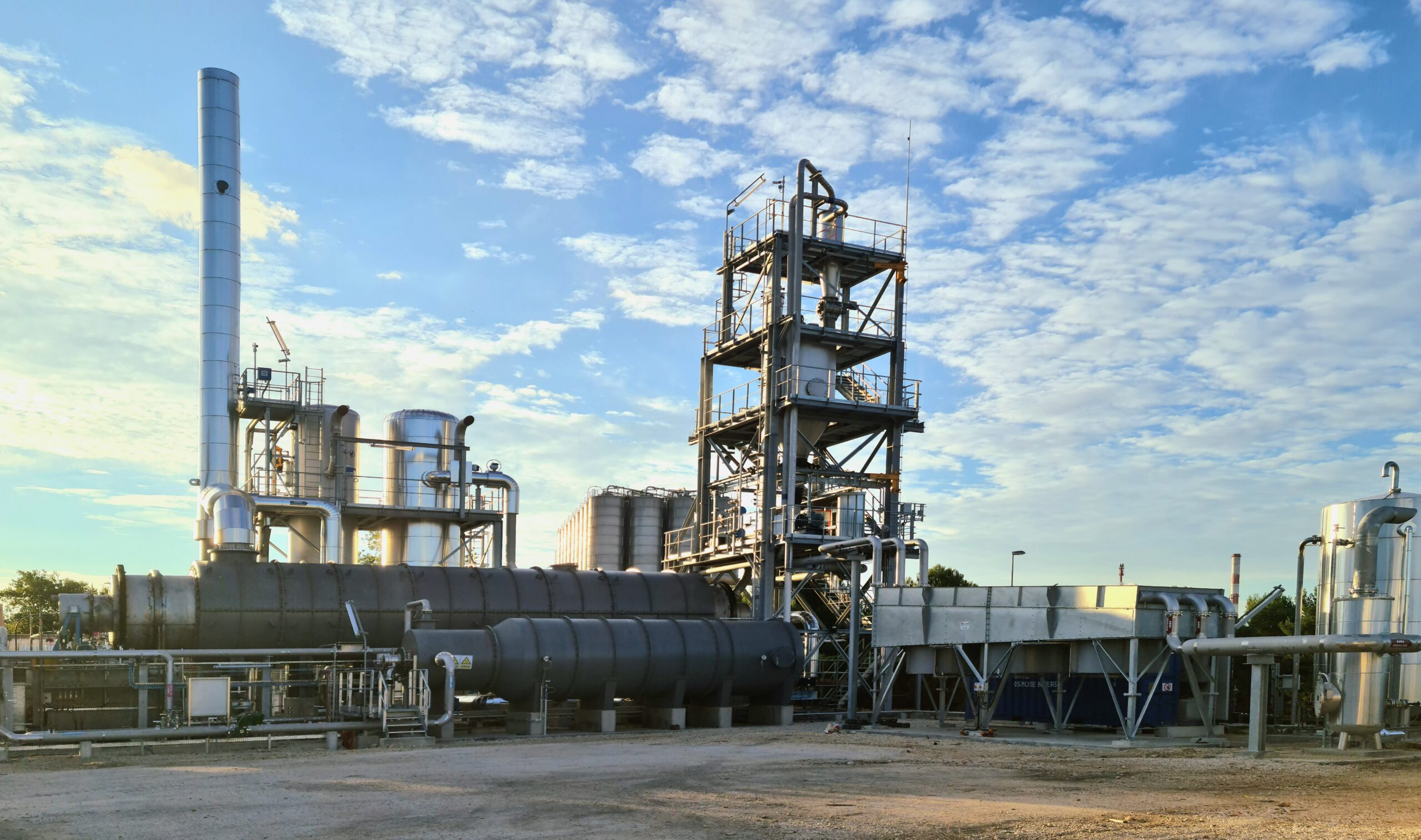
In 2018, the company expanded its strategy to focus more on the lithium-ion battery industry when it purchased a plant that makes acetylene-based additives in the southern French city of Berre-l’Étang, close to the port city of Marseilles. With the facility, Orion became the sole producer of acetylene-based conductives in Europe, and the company’s products have been qualified by market-leaders in the lithium-ion battery industry.
During the second half of 2025, Orion will open a plant in La Porte, Texas – close to Houston – that will be the only facility producing acetylene-based conductives in the U.S. The facility will effectively quadruple Orion’s manufacturing capacity of acetylene-based conductives.
By having a plant in the U.S., Orion will be able to significantly reduce shipping times – a major concern and expense in the industry – to gigafactories in Nevada, Georgia, Michigan and other states. Ocean transit alone can take up to 40 days, not including additional time for pre-carriage from production plants. From Orion’s plant in Texas, it will take just four days to reach Nevada and one to three days for other locations.
“Most importantly, shipping costs within the U.S. would likely be only 20% to 40% of the cost associated with overseas transport,” said Dr. Michael Rohde, director of Global Marketing for Batteries at Orion.
The company also uses furnace technology to make the conductive additive at its plant in Cologne, Germany. Orion plans to expand production in Asia.
“We will be where our customers are,” Dr. Rohde said. “We already have capacity in Germany and France, and we will soon add the U.S. and Asia.”
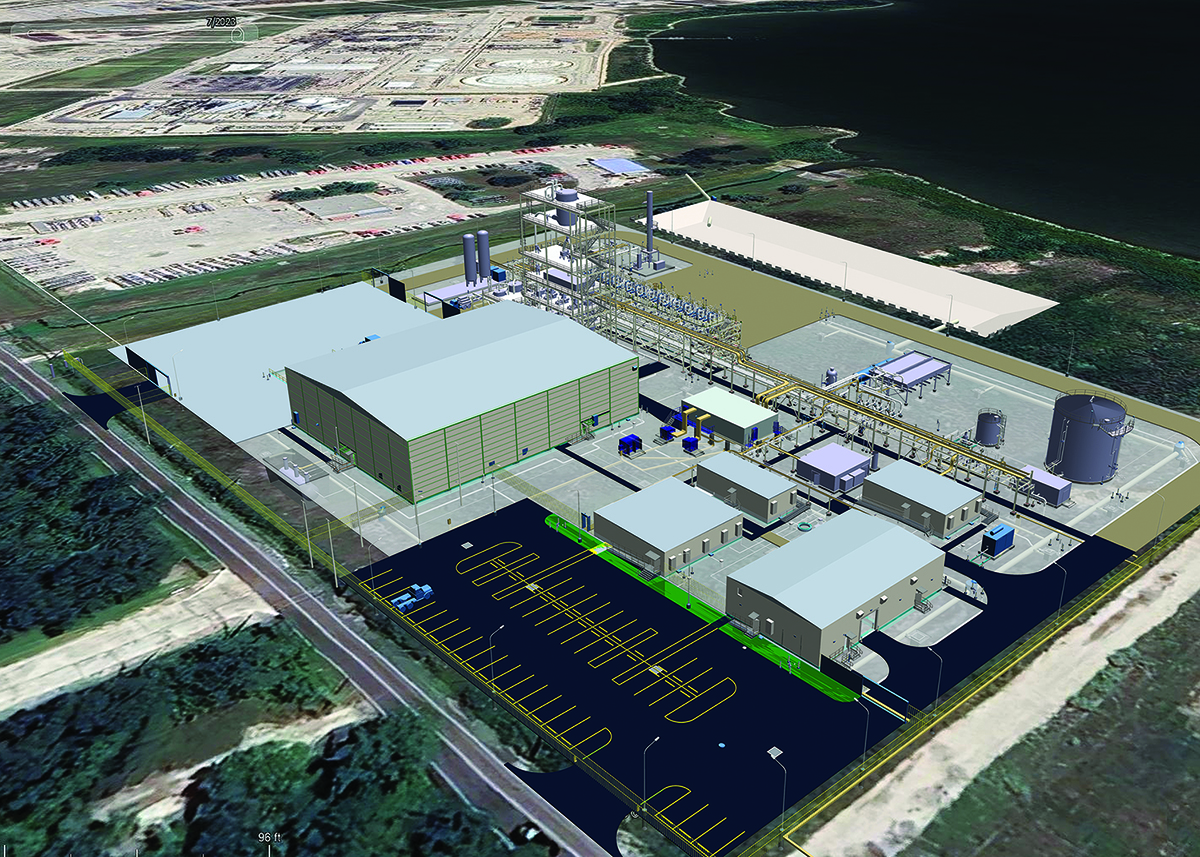
Expanding R&D
One of the most important points to understand about carbon black is that it is an essential specialty chemical – not a commodity – that must be engineered to fit the technical specifications of customers. So, it is vital for a company to have advanced research-and-development capabilities.
“What truly sets Orion apart from competitors is our customer-centric approach,” Dr. Rohde said. “We prioritize understanding and replicating our customer’s process conditions, enabling us to provide tailor-made solutions for their unique needs.”
Since buying the French plant in 2018, Orion has tripled the size of its laboratory. In 2023, the company opened a Battery Innovation Center at its main innovation hub in Cologne. The center includes a comprehensive suite of state-of-the-art production, testing and diagnostic equipment. It will accelerate Orion’s product and process development and foster close collaboration with customers to spur innovation and address evolving market needs.
“The laboratory has a wide variety of capabilities, including dispersion, slurry mixing and cell testing,” said Dr. Amaury Augeard, who brought to Orion more than a decade of experience working with batteries in the automotive industry when he joined the company as the head of innovation for batteries.
“We can also mimic customer-testing procedures, provide research and development that optimizes the performance of new grades as well as tailor make products and process development in close cooperation with our customers,” Dr. Augeard added.
The company has played a leading role in HiQ-CARB, an EU-funded project focused on developing more sustainable, affordable and high-quality carbon black additives for lithium-ion batteries. The consortium includes seven leading European industry players, research institutes and universities. In 2024, HiQ-CARB won third place in the EIT Innovation Awards, honoring Europe’s most promising innovators.
In summary, conductive additives are an essential component in modern batteries, ensuring high performance and long-term durability. Orion’s innovative approach, particularly with its acetylene-based conductive additives, sets new standards in both sustainability and quality for the battery industry.
With over 160 years of experience and a strong global presence, Orion is well-positioned to serve the growing demand for high-quality conductive additives across all regions. As the world shifts toward electrification, Orion continues to play a key role in supporting this transition with cutting-edge technology and a commitment to environmental responsibility.